1. Introduction
2. Key Model Framework
2.1
O&M Input on Design for New Building
2.2
Asset Information (Documentation)
2.3
Operation Procedures
2.4
Emergency Preparedness
2.5
Preventive Maintenance Procedures / Standards
2.6
Corrective Maintenance
2.7
Maintenance Record Management
2.8
Spare Parts Management
2.9
Addition, Alteration and Replacement (Planning and Implementation)
2.10
Incident Management
2.11
Environmental and Safety Management
2.12
Application of Technologies
2.13
Stakeholder Management
2.14
Information Management
2.15
Structure and Qualification of O&M Team
3. Innovative & Technology Initiatives
4. Industry Standards and Requirements
5. Useful Forms/ Check List - Samples
5.1
Recommended Minimum Monitoring Frequency for Different Water Quality Parameters for Cooling Tower System
5.2
Recommended Routine Inspection Checklist for Cooling Tower System
5.3
Recommended Routine and Preventive Maintenance Checklist for Cooling Tower System
5.4
Recommended List of Personal Protective Equipment
5.5
Operation and Maintenance Records for Cooling Tower System
5.6
Sample Independent Audit Report for Cooling Tower System
Introduction
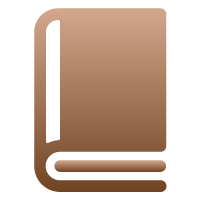
1.1 About This Best Practice Booklet
This Booklet is intended to outline the guiding principles on general, good and best practice to be considered during the design, construction, operation, maintenance, alteration, addition and replacement for the heat, ventilation and air conditioning (HVAC) installations in buildings to upraise the efficiency of asset management. It is designed for those users who are currently engaged in asset management of these installations in existing buildings or those who plan for new design and fitting-out works with these installations in new buildings. This Booklet should be read in conjunction with applicable ordinances and regulations in Hong Kong.
1.2 Target Audience
Target audiences of this Booklet are primarily for trade stakeholders including
building owners, building occupants, facility management professionals, maintenance agent or relevant
trade operators.
While in daily operations, the safety, system reliability, operational efficiency and sustainability of the assets rely on the daily operation and maintenance practices. In this regard, some information and recommendations to the interest of the trade stakeholders are outline in this Booklet as reference.
While in daily operations, the safety, system reliability, operational efficiency and sustainability of the assets rely on the daily operation and maintenance practices. In this regard, some information and recommendations to the interest of the trade stakeholders are outline in this Booklet as reference.
1.3 How to Use This Best Practice Booklet
This Booklet mainly covers 15 key attributes in the following stages in new and existing buildings:
The 15 key attributes are the key main considerations for achieving good or best performance in asset management of the HVAC Installations in buildings. Three levels of guiding principles, namely general, good and best practice, with associated examples of trade practices have been defined in each key attribute as reference. An additional chapter on "Innovative and Technology Initiatives" has also been included about the trend of technologies likely to be adopted to upraise the operation and maintenance service.
The figure provides an illustrative map for the 15 key attributes in different sections of the booklet.
A summary of the contents in this booklet is as follows:
The 15 key attributes are:
• Design, Construction and Commissioning,
• Operation and Maintenance and
• Alteration, Addition and Replacement.
• Operation and Maintenance and
• Alteration, Addition and Replacement.
The 15 key attributes are the key main considerations for achieving good or best performance in asset management of the HVAC Installations in buildings. Three levels of guiding principles, namely general, good and best practice, with associated examples of trade practices have been defined in each key attribute as reference. An additional chapter on "Innovative and Technology Initiatives" has also been included about the trend of technologies likely to be adopted to upraise the operation and maintenance service.
Level | Category | Description |
---|---|---|
Level 1 | General Practice | Involving general operating practices in fulfilling statutory requirements and aligning common practice in the trade industry |
Level 2 | Good Practice | Involving good operating practices with higher standard on enhancing either asset safety, system reliability, operational efficiency or sustainability |
Level 3 | Best Practice | Involving best operating practices with highest standard on asset management with use of innovative technologies or relevant life-cycle considerations |
The figure provides an illustrative map for the 15 key attributes in different sections of the booklet.
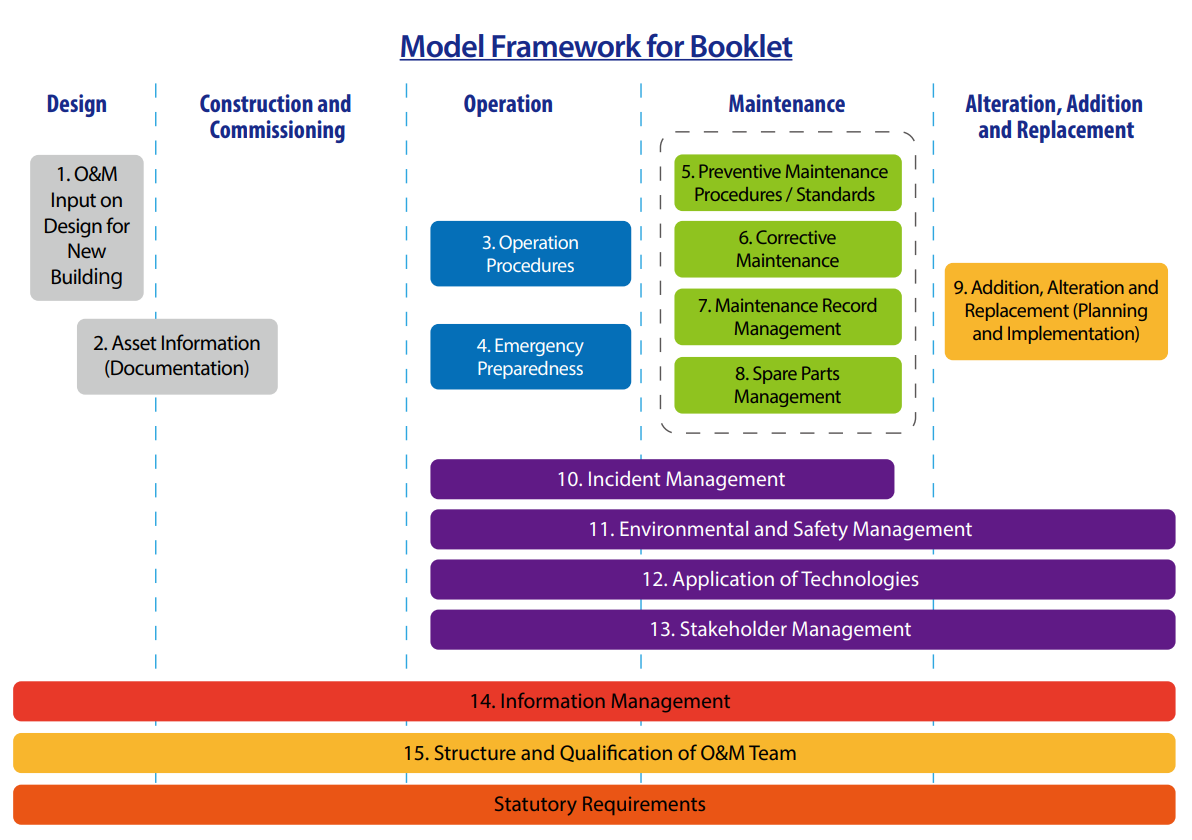
A summary of the contents in this booklet is as follows:
Section 1: Introduction to this Best Practice Booklet
Describes the important drivers for a building to perform efficiently and safely. This section explains what this Booklet is about, identifies key stakeholders, and directs the reader to specific sections. Section 2: Operation and Maintenance Best Practice Attributes
Describes the 15 key attributes for implementing good performance operation and maintenance of HVAC Systems in buildings. It defines three levels of practices namely, general, good and best practice, for each. The 15 key attributes are:
- O&M Input on Design for New Building - It is important for Design Engineers to consider accessibility and maintainability right from the planning and design of a facility, through its life cycle.
- Asset Information (Documentation) - Good documentation is essential for facilitating good operation and maintenance. This section describes the key documents that are required for the efficient operation and maintenance of HVAC Systems.
- Operation Procedures - All activities associated with the routine, day to day use, support, and maintenance of a building or physical asset; inclusive of normal/routine maintenance. O&M procedures at the system level do not replace manufacturers' documentation for specific pieces of equipment, but rather supplement those publications and guide their use.
- Emergency Preparedness - Being prepared for emergencies is important, and emergency management allow stakeholders to anticipate the types of potential hazards that could occur, and to think of ways to reduce the impact.
- Preventive Maintenance Procedures / Standards - Preventive Maintenance consists of a series of time-based maintenance requirements that provide a basis for planning, scheduling, and executing scheduled (planned versus corrective) maintenance. It is of a planned nature (versus the unplanned nature of Corrective Maintenance (CM)).
- Corrective Maintenance - This is an essential maintenance task performed to correct failures, breakdowns, malfunctions, anomalies or damages detected during inspections, or through monitoring, alarming, or reporting or any other source. The actions taken will aim to restore plant and equipment back into regular and required operation mode.
- Maintenance Record Management - This is a key part requiring efficient storage and management. Proper maintenance records minimise the number of expensive repairs, increase safeness in operation and enhance the visibility of equipment health.
- Spare Parts Management - Managing spare parts in an optimal way is an inherent and substantial part of O&M aimed at ensuring that spare parts are available in a timely manner for corrective maintenance in order to minimise the downtime of a system or equipment.
- Addition, Alteration and Replacement (Planning and Implementation) - This includes the analysis, procurement, management on additional, alteration as well as disposal and replacement of assets to meet the organisation's long term aims and objectives.
- Incident Management - This is the essential process to restore normal service operation as quickly as possible and limit the potential disruption caused by an incident.
- Environmental and Safety Management - The Building Owner has the ultimate legal and moral responsibility to ensure the health and safety of people in and around the building and for the protection of the environment around it.
- Application of Technologies - Integration and adaptation of new technologies with innovative methods to optimise system performance as well as operational effectiveness.
- Stakeholder Management - This is a critical component to the successful delivery of any service. It allows the correlation of stakeholders with potential known triggers, such as disruptions to their normal patterns and update on work progress, etc. It also estimates the impact that these reactions may have on your project or strategies and identifies whether targeted communication, mitigation or an alternative solution is required.
- Information Management - This concerns a cycle of organisational activity involving the acquisition of information from one or more sources, and the custodianship and distribution of that information to those who need it.
- Structure and Qualification of O&M Team - It is of critical importance that all O&M teams have a proper structure and their personnel have the relevant qualifications to perform the works in a safe, responsible and accountable manner.
Section 3: Innovative & Technology Initiatives
Describes the latest technology development in the use of innovative and technology initiatives adopted for O&M services for HVAC installations. Section 4: Industrial Standards and Requirements
Describes the summary of relevant statutory requirements involved in the O&M services for HVAC Installations Section 5: Useful Forms - Samples
Describes the commonly used forms / checklists adopted in O&M services for HVAC Installations. 1.4 Stakeholder Responsibilities
Trade stakeholders should be aware of their roles, responsibilities and
commitments to drive for implementation of the good and best practice, whenever applicable, for the
betterment of their routine asset management.
It is essential that all involved stakeholders shall work collaboratively as a team. While those involved for improving the current practices, they shall commit to facilitate and provide sharing on the necessary training, practical experience, knowhow and awareness of modern technology and the skills of optimising performance in their organisations.
The Building Owner should motivate and empower all Stakeholders to deliver efficiencies through O&M practices. The policies and strategies set by the Building Owner should drive the process for setting up the implementation of maintenance contracts and efficiency measures.
Tenants should adhere to the lease conditions when available, including Green Leases and Tenancy Fit-Out Guidelines, that express mutual expectations between Building Owners and Tenants with regards to operation, maintenance and performance requirements of buildings.
It is important for the FM to develop a maintenance regime that is geared towards delivering good outcomes in partnership with Maintenance Service Providers, who would benefit from the enhanced system efficiency. Forming good relationships and ensuring effective channels of communication including good documentation, is an important aspect to the process.
It is essential that all involved stakeholders shall work collaboratively as a team. While those involved for improving the current practices, they shall commit to facilitate and provide sharing on the necessary training, practical experience, knowhow and awareness of modern technology and the skills of optimising performance in their organisations.
1.4.1 Building Owner
The Building Owner has the ultimate responsibility for
operating and maintaining the base / central building services installations in adherence with all
applicable legal requirements.The Building Owner should motivate and empower all Stakeholders to deliver efficiencies through O&M practices. The policies and strategies set by the Building Owner should drive the process for setting up the implementation of maintenance contracts and efficiency measures.
1.4.2 Building Occupant (Tenant)
Tenants hold the responsibility to
ensure that the operation of the equipment is efficient, human behavioural patterns do not affect the
efficiency of the HVAC Systems, and that work carried out during tenancy fit-outs does not affect the
performance of base building services installations.Tenants should adhere to the lease conditions when available, including Green Leases and Tenancy Fit-Out Guidelines, that express mutual expectations between Building Owners and Tenants with regards to operation, maintenance and performance requirements of buildings.
1.4.3 Facilities Manager
The Facilities Manager (FM) is responsible for the
building management. The FM should implement the maintenance and environmental policies and strategies
set by the Building Owner in accordance with the allocated resources. The FM must take on the role of
the champion who leads the process for implementing changes that deliver better practices for the O&M of
the building. It is important for the FM to develop a maintenance regime that is geared towards delivering good outcomes in partnership with Maintenance Service Providers, who would benefit from the enhanced system efficiency. Forming good relationships and ensuring effective channels of communication including good documentation, is an important aspect to the process.
Subscribe for future updates
In order to subscribe to the newsletter or to activate e-mail notifications and content updates, you can follow few simple steps described below.It allows users to receive customized e-mail notifications when content is added or modified in EMSD.
Subscribe
x
Subscribe for future updates
We will only send you emails about the update that you subscribe to, and you can unsubscribe at any time.