1. Introduction
2. Design Considerations
3. Operation and Maintenance
4. Record/Documentation
5. Appendix A:Sample Checklist for Inspection and Testing of Solar PV Systems
Operation and Maintenance
3.1 Factors Affecting System Performance
(1)
There are several factors that will affect PV system performance over the operational lifetime:
a)
Soiling
The build-up of dust/dirt or other contaminants on the surface of the PV modules is known as soiling. This blocks the sunlight from reaching the solar cells and reduces the electricity generated.
Soiling is significant especially in the dry season and near the construction sites. In case the PV modules are installed where cleaning cannot be carried out easily, the PV modules should be suitably tilted to allow self-cleaning.
b)
Shading
The solar path changes throughout the year, and shading effect from the parapet, trees, or other obstacles becomes severe in winter. The performance of PV modules under varying light conditions will differ significantly, which in turn will have great impact on the yield of PV systems.
The shading effect from nearby obstacles, especially from the trees or new obstacles, should be checked.

c)
Mismatch Losses
Mismatch losses are caused by differences in the characteristics of PV cells or PV modules, and the overall system performance is determined by the lowest performing panel. The typical causes of mismatch losses include non-identical electrical characteristics, shading, differences in operating temperature and replacement of new PV modules. Besides, the PV modules degrade in different ways with long term aging and this leads to an increase in mismatch losses.
A like-for-like replacement should be made as far as possible. Products from different manufacturers, cell sizes or technologies are not recommended owing to different electrical characteristics of the panels.
d)
Major Components Breakdown
Major components failure, in particular inverter failure, may cause the whole system to break down in the worst-case scenario. Bypass and blocking diodes failure will cause poor system performance. Cable damage will also cause the breakdown of the solar system. Regular checking and immediate replacement are critical.
e)
Solar Irradiance
The amount of electricity generated from a PV system depends on the amount of irradiance falling on the PV module surface. The tilt and azimuth angles of the PV module will affect the annual solar irradiation received.
The tilt and azimuth angles will be changed from time to time and should be checked regularly, especially after typhoon attacks.
3.2 Operation Procedures
3.2.1 General Practice
(1)
The system operator or the Contractor of a solar PV system should read the operation instructions recommended by the manufacturer/supplier. The owner should properly store and keep all the technical documents for future reference.
(2)
The owner should arrange regular inspections and routine maintenance and functional check of the solar PV system as stipulated in Section 3.4 below.
(3)
The owner can perform general cleaning work by using clean water and soft cloth or sponge on the PV module surface on a regular basis to maximise the electricity generation, whilst electrical work on the PV system must be carried out by a REC/REW.
(4)
For safety precautions for works on the electrical installation, refer to the CoP.
(5)
Before operating the PV system, the REC/REW should read all instructions for each product and the following procedures for electrical disconnection and restoration must be carried out prior to and after carrying out any electrical work on the PV system:
a)
Notify the owner/representative of the PV system that the system will be shut down
b)
Isolation of supply from PV system and the Grid
•
Switch OFF the lockable main switch of the PV system at the Grid supply side to isolate the supply from the Grid. Apply lock and affix appropriate warning notice(s)
•
Switch OFF the DC circuit breakers, inverters and/or associated isolation switch(es) at PV system side to isolate the supplies from PV system. Apply lock and affix appropriate warning notice(s)
•
The keys for all isolation points shall be kept by the responsible REC/REW
c)
Verification of complete de-energisation of the system
d)
After completion of work, the REC/REW shall inspect, test and certify that the installation is safe for energisation
e)
Restoration of supply from PV system and the Grid
•
Remove the warning notice(s) and unlock the isolation switch(es) at PV system side. Switch ON the DC circuit breakers, inverters and/or isolation switch(es) to restore supply from PV system
•
Remove the warning notice(s) and unlock the lockable main switch of the PV system at the Grid supply side. Switch ON the main switch to restore supply from the Grid
•
Notify the owner/representative of the PV System, the REC and other relevant parties after work completion
(6)
Proper access tools such as ladders should be provided and fall arrest systems should be used.
3.3 Emergency Preparedness
3.3.1 General Practice
(1)
An up-to-date emergency contact list shall be provided and attached at the location near the installation showing the following items:
•
Name of the contact person or company
•
Telephone number
(2)
In case of emergency, the PV system shall be shut down and isolated from the Grid. Refer to Section 3.2 above for operation procedures of isolation of PV systems and the Grid.
3.3.2 Best Practice
(1)
Emergency plan/procedures including the communication flow between the PV system owner, system operator and the maintenance contractor, should be provided on site. The emergency plan/procedures should be reviewed on a regular basis.
3.4 Preventive Maintenance
3.4.1 General Practice
(1)
To maximise the yield of a PV system in its operational period, routine preventive maintenance work is essential. All preventive maintenance work shall be read in conjunction with the maintenance manual recommended by the manufacturer.
(2)
The PV system owner or system operator shall be notified about the testing or shutdown of the system.
(3)
The electrical work for the PV system shall only be carried out by a REC/ REW who shall carry out a risk assessment before commencement of work.
(4)
All testing instruments shall be calibrated by an accredited laboratory before use.
(5)
For safety precautions for works on the electrical installation, please refer to the CoP.
3.4.2 Best Practice
(1)
The maintenance schedule and procedures shall be regularly reviewed and updated against the latest statutory requirements, international standards and maintenance history.
3.4.3 Preventive Maintenance Schedule
(1)
Preventive maintenance schedule for a PV system is recommended as below:
Components/ equipment | Description | Action | Recommended Frequency | General Practice | Best Practice |
---|---|---|---|---|---|
PV Modules | Warning notice inspection | Check for warning signs and labels and replace if necessary | Annual | • | • |
General cleaning | Clean the PV modules with water to remove dust, debris and other contaminants on the module surface | Quarterly | • | • | |
PV module inspection | Check PV modules, junction boxes, cables and connectors for damage, such as burn marks, bubble formation, cracking, broken glass, discoloration, corrosion, etc. | Bi-annual to annual | • | • | |
Check for any loose cable connection | • | • | |||
Hot-spot inspection | Use infrared camera to inspect for hot spots | Annual | • | ||
Bypass diode | Check the functioning of the bypass diodes | Annual | • | ||
Bonding conductor inspection and testing (PV metallic frame to PV metallic frame) | Check bonding conductor conditions | For every 5 years or as required by Periodic Inspection, Testing and Certification (PITC) | • | • | |
Continuity test for protective conductors and/ or equipotential bonding | • | • | |||
Module performance testing | Check solar irradiance and the power output from the PV modules and compare the readings with calculated power output to verify the PV modules performance and identify any defective modules | Annual (except systems with micro-inverters or power optimisers installed for each PV module) | • | ||
Supporting Frames and Structures | Supporting system inspection | Check integrity of the penetration, physical connections and fixing components to make sure each PV module is securely fixed | Annual (Remark 1) | • | • |
Corrosion inspection | Check all hardware for signs of corrosion and remove rust; re-paint and replace if necessary | Annual | • | • | |
Bonding conductor inspection and testing (PV metallic frame to supporting frames, supporting frames to earth terminal) | Check bonding conductor conditions | For every 5 years or as required by PITC | • | • | |
Continuity test for protective conductors and/or equipotential bondings | • | • | |||
PV Arrays | Array inspection | Check for abnormal position and movement of PV arrays | Annual (Remark 1) | • | • |
Electrical measurement | Check open-circuit voltage, operating current of a series of strings to ensure PV modules are working properly | Annual | • | ||
DC Side of System | Warning notice inspection | Check for warning signs and labels and replace if necessary | Annual | • | • |
Cable inspection | Check cable for signs of cracks, defects, pulling out of connections, loose connections, overheating, arcing, short or open circuits, and earth faults | Annual | • | • | |
DC disconnect switch/circuit breakers inspection | Check position of disconnect switches and circuit breakers and fuse status | Annual | • | • | |
Surge arrester inspection | Check surge arrester conditions and replace as per manufacturer’s recommendations | For every 5 years or as per manufacturer's recommendation | • | • | |
Combiner box inspection | Check for corrosion, intrusion of water or insects | Annual | • | • | |
DC circuit test | Carry out DC circuit tests including insulation test, polarity test, and operation of protection devices or as specified in CoP | For every 5 years or as required by PITC | • | • | |
Inverters | Warning notice inspection | Check for warning signs and labels and replace if necessary | Annual | • | • |
Dust removal from heat rejection fins and ventilation fan if provided | Check ventilation conditions and clean the dust of inverter cabinet | Bi-annual to annual | • | • | |
Cable wiring inspection | Check for loose cable connections | Annual | • | • | |
Operation temperature inspection | Check for abnormal operation temperature | Bi-annual to annual | • | ||
Functional test | Check functionality such as automatic disconnection upon loss of grid power supply | Bi-annual to annual or as per manufacturer's recommendation | • | • | |
Measure the input and output power to ensure the inverters are working properly | Annual | • | |||
AC Side of System | Warning notice inspection | Check for warning signs and labels and replace if necessary | Annual | • | • |
Cable inspection | Check cable for signs of cracks, defects, pulling out of connections, loose connections, overheating, arcing, short or open circuits, and earth faults | Annual | • | • | |
Distribution board inspection | Check for corrosion, intrusion of water or insects | Annual | • | • | |
AC disconnect switch/circuit breakers inspection | Check position of disconnect switches and circuit breakers and fuse status | Annual | • | • | |
Surge arrester inspection | Check surge arrester conditions and replace as per manufacturer’s recommendations | For every 5 years or as per manufacturer's recommendation | • | • | |
AC circuit test | Carry out AC circuit tests including insulation test, polarity test, operation of protection devices and tripping time of residual current device/residual circuit breaker with overcurrent protection (RCD/RCBO) or as specified in CoP | For every 5 years or as required by PITC | • | • | |
Isolation Transformer | Warning notice inspection | Check for warning signs and labels and replace if necessary | Annual | • | • |
Isolation transformer inspection | Inspect the conditions of isolation transformers and clean the dust from heat rejection fin | Annual | • | • | |
Functional test | Check the primary and secondary voltage/current/ power/frequency, carry out insulation test | Annual | • | • | |
System Test | Check the power quality of PV system | Check the total harmonic current distortion, DC injection current | For every 5 years or as required by PITC | • | • |
Anti-islanding test (for grid-connected system) | Check the voltage and current waveforms by opening the isolation switch and check the anti-islanding time is sufficient in accordance with power company’s requirements | For every 5 years or as required by PITC | • | • | |
Earthing Protection System | Warning notice inspection | Check for warning signs and labels and replace if necessary | Annual | • | • |
Visual inspection | Check for loose earthing conductor connections | Annual | • | • | |
Continuity test | Check continuity of the earthing conductors and the earth fault loop impedance of the PV system | For every 5 years or as required by PITC | • | • | |
Check the insulation of the earthing cables to the live cables | • | • | |||
Check the earth fault loop impedance | • | • | |||
Lightning Protection System | Warning notice inspection | Check for warning signs and labels and replace if necessary | Annual | • | • |
Visual inspection | Check bonding conductor conditions and any loose bonding conductor connection | Annual | • | • | |
Continuity test | Check continuity of the bonding conductors to lightning system | For every 5 years or as required by PITC | • | • | |
Instrument | Instrument inspection | Check the monitoring instruments (e.g., pyranometers, weather sensors) to make sure they are operational | Annual | • | |
Instrument calibration | Calibrate or replace instruments, weather sensors, and meters | Annual | • | ||
System Monitoring | Operation and performance monitoring | Monitor the operation, performance, alarms and alert parameters | On-going | • | |
Check PV system monitoring | Check building management system for PV system, check hardware for signal interface and upgrade software as necessary | Annual | • | ||
Log record | Maintain a log of cumulative power delivery (kWh to date) and generate a chart of power against date | Monthly | • | ||
Performance checking | Check the instant solar irradiation and the energy output from the PV system and compare the system efficiency with the design figure | Annual | • | ||
Battery System (for off-grid system) | Warning notice inspection | Check for warning sign and label and replace if necessary | Annual | • | • |
Battery enclosure cleaning | Container or enclosure cleaning | Annual | • | • | |
Visual inspection | Check the battery bank for chemical leakage, cracks, bulging, integrity of battery enclosure, and support structure | Annual | • | • | |
Corrosion inspection | Check all hardware for signs of corrosion and remove rust and re-paint if necessary | Annual | • | • | |
Ventilation inspection | Check ventilation conditions of the battery room and remove the dust on the louvres | Annual | • | • | |
Electrical connection inspection | Check all electrical connections on battery bank for loose electrical connections | Annual | • | • | |
Battery capacity testing | Test battery capacity | Annual | • | ||
Battery charge controller | Check the overcharging and over-discharging functions | Annual | • | • | |
Others | Roof penetration | Check the watertightness | Annual | • | |
Vegetation growth | Check for any vegetation growth or other shade items | Annual | • |
Remark 1:
Precautionary measures against damage to PV system, visual inspection before and after typhoon shall be carried out to make sure the system is in safe conditions.
3.5 Corrective Maintenance
3.5.1 General Practice
(1)
Refer to the CoP for safety precautions for work on the electrical installations.
(2)
Whenever the major components are replaced, the following shall be checked:
a)
The maximum DC power, voltage and current of the PV string with new PV module installed shall be checked and not exceeding the inverter limit
b)
Using different electrical characteristics of PV module at one inverter or connecting to the same MPP tracker should be avoided
c)
The operating voltage and the current carrying capacity of cables and rating of circuit breakers shall be checked before replacement
d)
In case multiple inverters are replaced by single inverters with higher rating or vice versa, the maximum DC power, voltage and current at the DC input of the inverter shall be checked
e)
The polarity of all DC cables shall be checked to ensure the cables are correctly identified and correctly connected into system devices such as switching devices or inverters
f)
Bonding conductors shall be checked after any replacement to ensure the earthing system is in order
(3)
Maintenance records and technical information shall be updated after replacement.
(4)
In case the system is grid-connected and registered as generating facility under the Electricity Ordinance (Cap.406), the power companies shall be informed of any changes in the installed capacity of the PV system after replacement, and Form GF2 shall be submitted to the EMSD in accordance with the Electricity (Registration) Regulations.
3.5.2 Best Practice
(1)
Corrective maintenance carried out during the night or low irradiation hours should be considered as the best practice as the overall power generation is not affected.
(2)
The response time for corrective maintenance or conditions that have introduced a safety problem should be addressed and reviewed regularly.
3.6 Spare Parts Management
3.6.1 General Practice
(1)
The stocking levels of spare parts depend on the following parameters:
a)
Frequency of failure
b)
Impact of failure
c)
Cost of spare parts
d)
Degradation of spare parts over time
e)
Equipment reliability
(2)
PV system operators shall maintain an updated list of spare parts suppliers and sufficient spare parts. The minimum spare parts are listed below:
a)
Circuit breakers (including fuses)
b)
Switches
c)
Screws and other supplies and tools
d)
Cable ties
(3)
The solar PV system operator should formulate the spare part list according to their needs.
3.6.2 Best Practice
(1)
The type and quantity of on-site spare parts should be derived from faulty history and maintenance records and reviewed regularly.
(2)
The obsolescence of spare parts and availability of substitutes should be reviewed regularly.
3.7 Safety and Environmental Management
3.7.1 General Practice
(1)
Prior to any maintenance work of PV system, it is necessary to:
a)
Identify all possible risks
b)
Determine the work practices that will be undertaken to remove the risks, or to minimise the risks if they cannot be removed altogether
c)
Communicate with all staff working on-site about the risks and how they will be removed or minimised
3.7.2 Best Practice
(1)
The PV system operator should establish an Environment Management System (e.g., ISO 14001) and a Safety Management System (e.g., OHSAS 18001 or ISO 45001).
3.8 Structure and Qualifications of O&M Teams
3.8.1 General Practice
(1)
An organisation chart with the names and contact numbers of the O&M team should be provided and each technical staff member shall be a REW.
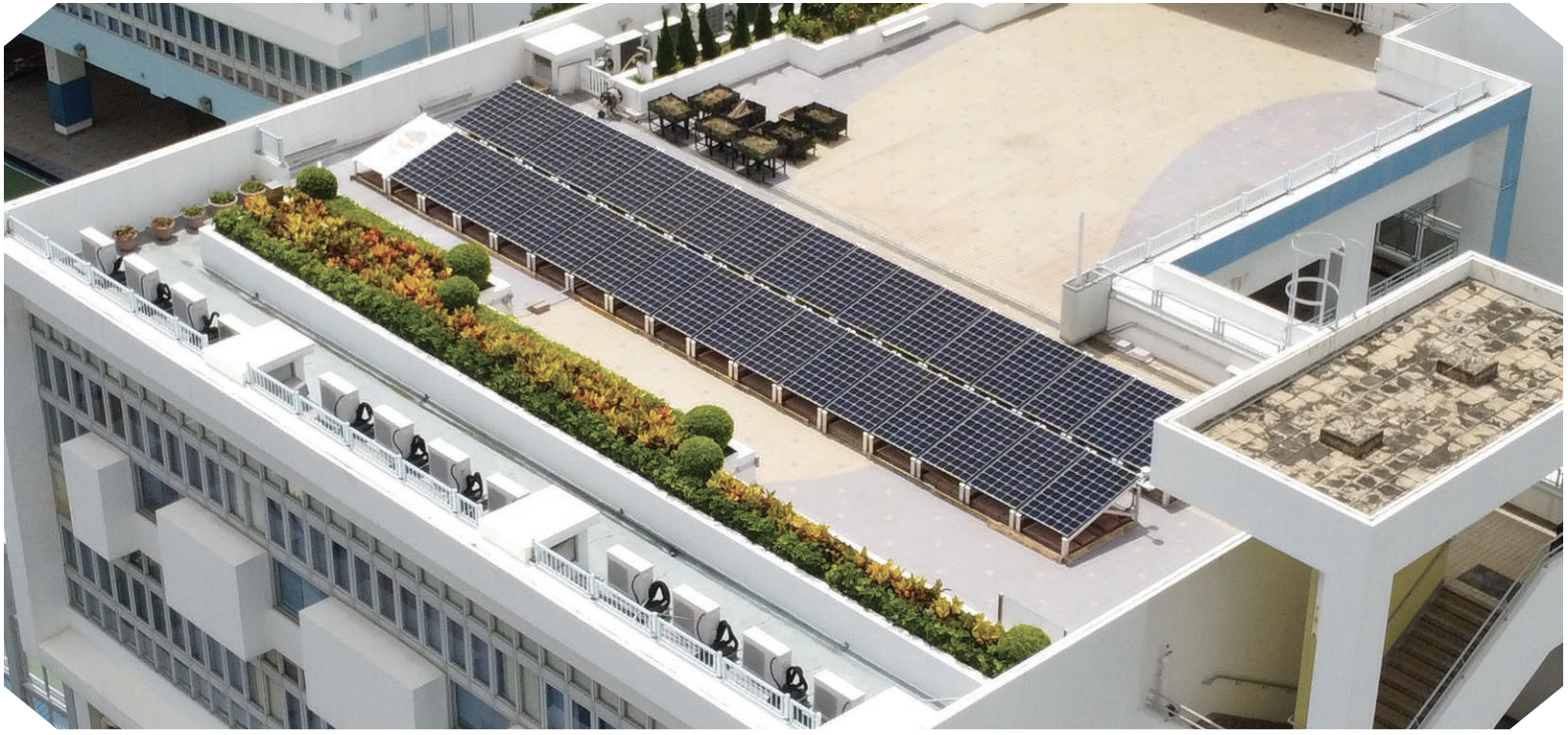
Subscribe for future updates
In order to subscribe to the newsletter or to activate e-mail notifications and content updates, you can follow few simple steps described below.It allows users to receive customized e-mail notifications when content is added or modified in EMSD.
Subscribe
x
Subscribe for future updates
We will only send you emails about the update that you subscribe to, and you can unsubscribe at any time.
Last revision date: 6 Jun, 2023 This site is best viewed with: Chrome or Firefox © 2023 emsd.gov.hk