1. Introduction
2. Design Considerations
3. Operation and Maintenance
4. Record/Documentation
5. Appendix A:Sample Checklist for Inspection and Testing of Solar Water Heating Systems
Operation and Maintenance
3.1 Factors Affecting System Performance
(1)
There are several factors that will affect solar water heating system performance over its operational lifetime:
a)
Soiling
Dusty and soiled collectors perform poorly. Soiling is significant especially in the dry season and near construction sites. Periodic cleaning is essential to maintain system performance.
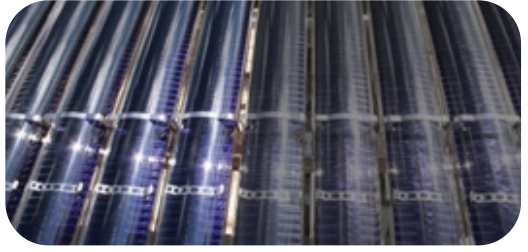
b)
Shading
Shading will affect the performance of solar collectors. Vegetation growth or new constructions nearby may induce shading that was not there when the collectors were installed. Regular visual checking for shading during daytime is important.
c)
Damage of Solar Collectors
A broken glazing is a major factor affecting the performance of a solar water heating system. Broken glazing may be due to thermal expansion. The interior of the collector, particularly the absorber and insulation, must be protected from inclement weather.
d)
Overheating
During periods of high solar irradiance and low hot-water demand, overheating can occur in the solar collectors or storage tanks. Thermal expansion or excessive pressure can burst the associated piping of the storage tank. Overheating may produce steam within the system and make the system inoperable. Therefore, protection against overheating must be considered.
The most common methods to prevent overheating are:
•
Stopping circulation in the collection loop until the storage temperature decreases
•
Replacing the overheated water with cold makeup water
e)
Leakage
Leakage at solar collectors, valves, pipe fittings may occur due to thermal expansion or natural deterioration, making the system inefficient.
f)
Scaling
Scaling in a solar water heating system (collectors, pipes, etc.) will affect the system performance in a few ways. In Hong Kong, scaling might occur after a few years of operation though the city’s fresh water is soft in nature.
3.2 Operation Procedures
3.2.1 General Practice
(1)
The system operator or the Contractor of a solar water heating system should read the operation instructions recommended by the manufacturer/supplier.
(2)
The owner can perform simple cleaning work by using clean water on the solar collector surface on a regular basis whilst the waterworks for a solar water heating system shall only be carried out by a LP and the associated electrical work shall be carried out by a REC/REW. Safety measures against high temperature along the system must be carried out before system inspection and maintenance as the operation temperature of a solar water heating system cannot be controlled.
(3)
Before operating the solar water heating system, the system operator or the Contractor should read all instructions for each product. The following procedures for water disconnection and restoration must be carried out prior to and after carrying out any maintenance work of the solar water heating system:
a)
Notify the owner/representative of the solar water heating system that the system will be shut down
b)
Isolation of the solar water heating system from the main hot water supply system
•
Switch OFF the hot water circulation pump. Apply lock and affix appropriate warning notice(s)
•
The keys for all isolation points shall be kept by the responsible REC/REW
c)
Verification that the system is completely switched OFF
d)
After completion of work, the system operator or the Contractor shall inspect, test and certify that the installation is safe for restoration
e)
Restoration of the solar water heating system from the main hot water system
•
Remove the warning notice(s) and unlock the isolation switch(es) of the hot water circulation pump. Switch ON the isolation switch(es) to restore the solar water heating system
•
Notify the owner/representative of the solar water heating system and other relevant parties after work completion
(4)
The storage tank is to be completely filled with water and all air is to be vented before energising.
(5)
Control of Legionella
To avoid the risk of bacterial growth in water, all solar pre-heated water shall be designed to pass through a local heater or hot water system and heat up to at least 60 °C for at least 5 minutes prior to being discharged to the distribution system under normal loading conditions. The proper design, operation and maintenance of building facilities for prevention of Legionnaires’ disease are addressed in the “Code of Practice for Prevention of Legionnaires’ Disease”. The reader may refer to the technical guidelines for further information.
(6)
Proper access tools such as ladders should be provided and with the use of fall arrest systems.
(7)
If the fluid of the whole solar heating system has to be drained off for overhaul for a considerable period of time, it is suggested to cover up the solar collectors to avoid high temperature building up on the absorbing surface which may accelerate material ageing and pipe joints leakage.
(8)
Idling the solar water heating system for a long period of time should be avoided to prevent stagnant water and if this cannot be avoided, it is recommended that the power to the circulation pump shall be disconnected and that the solar collectors are covered with a blanket or other means to prevent heat gain from the sun leading to system overheating.
3.3 Emergency Preparedness
3.3.1 General Practice
(1)
An up-to-date emergency contact list shall be provided and attached at the location near the installation showing the followings items:
•
Name of the contact person or company
•
Telephone number
(2)
In case of emergency, the power to the circulation pump and the valve(s) for shutting off the flow through the collector shall be disconnected to isolate any electricity or fluids from entering the solar water heating system.
3.3.2 Best Practice
(1)
Emergency plan/procedures including the communication flow between the solar water heating system owner, system operator and the maintenance contractor, should be provided on site. The emergency plan/procedures should be reviewed on a regular basis.
3.4 Preventive Maintenance
3.4.1 General Practice
(1)
All preventive maintenance work shall be read in conjunction with the operation and maintenance (O&M) manual for E&M installations with similar system configuration as the plumbing system as well as the maintenance manual recommended by the manufacturers.
(2)
The solar water heating system owner or the system operator shall be notified for the testing or shutdown of the system.
(3)
As the operation temperature of a solar water heating system cannot be controlled, safety measures against overheating must be carried out before system inspection and maintenance.
(4)
Maintenance of a solar water heating system shall only be carried out by an appropriate LP who shall conduct a risk assessment before commencement of work.
(5)
All testing instruments shall be calibrated by an accredited laboratory before use.
3.4.2 Best Practice
(1)
The maintenance schedule and procedures shall be regularly reviewed and updated against the latest statutory requirements, international standards and maintenance history.
3.4.3 Preventive Maintenance Schedule
(1)
Preventive maintenance schedule for a solar water heating system is recommended as below:
Components/ equipment | Description | Action | Recommended Frequency | General Practice | Best Practice |
---|---|---|---|---|---|
Solar Collectors | General cleaning | Clean the collectors (when they are cool) to remove dust, debris and other contaminants on the collector surface | Bi-annual to annual | • | • |
Visual inspection | Check the collectors for cracked, broken or deformed glass, shading, deterioration of absorber paint/coating, tubes and insulation | Annual | • | • | |
Check the surface temperature of the absorbers for abnormal temperature | Annual | • | |||
Check for excessive condensation or outgassing under glazing | Annual | • | |||
Check the frames for corrosion | Annual | • | • | ||
Check the earthing conductor conditions for collectors with sensors | • | • | |||
Flow rate | Test the flow rate for compliance with manufacturer’s recommendations and the temperature of each collector group in the array | Annual | • | ||
Leakage inspection | Check the absorbers and pipes for any leakage | Annual | • | • | |
Descaling | Remove scaling inside pipework | Every 10 years | • | ||
Supporting Frames | Mounting system inspection | Check the physical connections and fixing components to make sure the solar collectors and pipework are securely fixed | Annual (Remark 1) | • | • |
Corrosion inspection | Check all hardware for signs of corrosion, remove rust; re-paint and replace if necessary | Annual | • | • | |
Solar Collector Arrays | Array inspection | Check for abnormal position and movement of solar collectors | Annual (Remark 1) | • | • |
Check hot water flow rate of collector arrays | Annual | • | |||
Heat Transfer Fluids | Heat transfer fluid inspection | Check heat transfer fluid conditions, concentration and degradation for indirect type; refill the heat transfer fluid if necessary | Annual | • | |
Check the water quality for direct type | • | • | |||
Check that provisions are made for draining and filling the system (air vents, drains, pipes correctly graded in-between) | • | • | |||
Pipework | Visual inspection | Check pipework for signs of cracks, defects and leaks, damage, blockage, or degradation of thermal insulation | Annual | • | • |
Hanger inspection | Inspect for signs of defects, sagging, cracks; replace if necessary | Annual | • | • | |
Air lock | Check the air locks or blockages of the pipework | Annual | • | ||
Drainage inspection | Check signs of deformation not holding slopes to drain | Annual | • | • | |
Operation temperature inspection | Check for abnormal operation temperature, stop circulation in the collection loop and release the excessive pressure inside pipework if any | Bi-annual to Annual | • | ||
Descaling | Remove scaling from the pipework | Every 10 years | • | ||
Valves | Visual inspection | Check valves for any damage, leakage, getting stuck or sign of corrosion; check valve settings and valve position | Monthly | • | • |
Valves functional test | Test valve operation according to the O&M manual and manufacturer's recommendations | Monthly | • | • | |
Strainers | General cleaning | General cleaning and check for signs of corrosion and getting stuck | Bi-annual | • | • |
Heat Exchangers | Visual inspection | Check the heat exchanger for signs of leakage or corrosion and the associated supports | Annual | • | • |
Flow rate | Test the flow rate for compliance with manufacturer’s recommendations | Annual | • | ||
Descaling | Remove scaling from the heat exchangers | Every 10 years | • | ||
Thermal Storage Tanks | Visual inspection | Check storage tanks for cracks, leaks, rust or signs of corrosion | Annual | • | • |
Check the insulation for damage or degradation | Annual | • | |||
Pressure relief | Check the system pressure and temperature, depressurise the excessive system pressure if any | Annual | • | ||
Water discharge | Discharge water inside | Bi-annual | • | ||
Descaling | Remove scaling from the thermal storage tanks | Every 10 years | • | ||
Reverse heating prevention (if backup heating is provided) | Check that provisions have been made to prevent reverse heating of the solar thermal storage by the domestic hot-water backup heater | Annual | • | • | |
Backup heating (if provided) | Check the thermostat and control of the backup heating element | Annual | • | ||
Expansion Tanks | Leakage check | Check the expansion tanks with diaphragms in by briefly depressing the Schrader valve for leaks of fluid | Annual | • | • |
Pumps | General cleaning | General cleaning and re-paint | Annual | • | • |
Visual inspection | Check that the electrical connections are securely fastened and the earth bonding conductors are properly connected | Annual | • | • | |
Check the piping connections for leakages | • | • | |||
Lubrication | Lubricate the moving parts | Annual | • | • | |
Functional and operation test | Check that the pumps are operating correctly without abnormal movement or water leakage | Annual | • | • | |
Check the pressure and flow to ensure the operation condition of the pump is in order | • | • | |||
Make-up Water Tanks | General cleaning | Drain and flush out the tank to remove sediment | Annual | • | • |
Visual inspection | Check the water tank for cracks, leaks, rust or signs of corrosion | Annual | • | • | |
Controls, Sensors and Meters | Visual inspection | Check operational indicators of temperature and pressure to ensure proper operation of the pump and controls | Annual | • | • |
Check the sensor wiring for avoidance of losing connection | Annual | • | • | ||
Check the accuracy of the sensors and controls, recalibrate if necessary | Annual | • | • | ||
Functional test | Check that controls, water level sensors, temperature sensors are operating sensibly | Annual | • | • | |
Pump control panel inspection | Open pump control panel box and check that no fuses/MCBs have blown and all electrical connections are tight | Annual | • | • | |
Check for water incursion and corrosion damage | Annual | • | • | ||
Pump control panel inspection | Conduct functional tests of the pump panel control | For every five years or as required by PITC | • | ||
Conduct functional tests of isolation switches and protection devices | • | • | |||
Dust removal from heat rejection fins | Check ventilation conditions and dust cleaning from heat rejection fins | Annual | • | • | |
Pressure relief valves | Check and make sure the valve is not stuck or closed | Annual | • | • | |
Safety and Warning Notices and Labels | Safety and warning notice inspection | Check for warning signs and labels and replace if necessary | Annual | • | • |
Labels | Check the tags or labels which indicate the positions or flow direction at each valve and pipe | Annual | • | • | |
Instruments | Instrument inspection | Check the monitoring instruments (e.g., temperature sensors) to make sure they are operational | Annual | • | |
Instrument calibration | Calibrate instruments by an accredited laboratory. Replace instruments, temperature sensors, and meters as necessary | Annual | • | ||
System Monitoring and Data Logging System | Operation and performance monitoring | Monitor the operating status, flow rate, temperature, alarms and alert parameters | On-going | • | |
Check system monitoring | Check Building Management System for the solar water heating system, check hardware for signal interface and upgrade software as necessary | Annual | • | ||
Log record | Maintain a log of cumulative electrical energy consumption (kWh to date), operating temperature and flow rate against date | Monthly | • | ||
Performance checking | Check the monthly mean in-plan solar irradiation, monthly mean solar energy absorbed by system and monthly electrical energy consumption of circulation pump | Annual | • |
Remark 1:
Precautionary measures against damage to solar collector array, and visual inspection before and after typhoon shall be carried out to make sure the system is in safe condition.
3.5 Corrective Maintenance
3.5.1 General Practice
(1)
All plumbing work shall be carried out by an appropriate LP.
(2)
Whenever the major components are replaced, the following shall be checked:
a)
Specification of solar collectors
b)
Water valves
c)
Control set point
d)
Function and operation
(3)
Maintenance records and technical information shall be updated after replacement.
(4)
Before the replacement of system components, drain the water from the hot water pipe and make sure the water to the water heater has been completely shut off.
(5)
Statutory submission to the WSD may be required if water pipework is changed during maintenance. The reader should refer to the Waterworks Ordinance.
3.5.2 Best Practice
(1)
Corrective maintenance carried out during the night or low irradiation hours shall be considered as best practice in avoiding high temperature.
(2)
The response time for corrective maintenance or conditions that introduce a safety problem should be addressed and reviewed regularly.
3.6 Spare Parts Management
3.6.1 General Practice
(1)
The stocking levels of spare parts depend on the following parameters:
a)
Frequency of failure
b)
Impact of failure
c)
Cost of spare parts
d)
Degradation of spare parts over time
e)
Equipment reliability
(2)
Solar water heating system operators shall maintain an updated list of spare parts suppliers and sufficient spare parts. The minimum spare parts are listed below:
a)
Temperature/pressure relief valve
b)
Air vent
(3)
The solar water heating system operator should formulate the spare part list according to their needs.
3.6.2 Best Practice
(1)
The type and quantity of on-site spare parts should be derived from fault history and maintenance records and reviewed regularly.
(2)
The obsolescence of spare parts and the availability of substitutes should be reviewed regularly.
3.7 Safety and Environmental Management
3.7.1 General Practice
(1)
Prior to any maintenance work of solar water heating system, it is necessary to:
a)
Identify all possible risks
b)
Determine the work practices that will be undertaken to remove the risks, or to minimise the risks if they cannot be removed altogether
c)
Communicate with all staff working on-site about these risks and how they will be removed or minimised
3.7.2 Best Practice
(1)
The solar water heating system operator should establish an Environment Management System (e.g., ISO 14001) and a Safety Management System (e.g., OHSAS 18001 or ISO 45001).
3.8 Structure and Qualifications of O&M Teams
3.8.1 General Practice
(1)
An organisation chart with the names and contact numbers of the O&M team should be provided. The technical staff for the water supply system shall be LPs while those for the electrical system shall be REWs.
Subscribe for future updates
In order to subscribe to the newsletter or to activate e-mail notifications and content updates, you can follow few simple steps described below.It allows users to receive customized e-mail notifications when content is added or modified in EMSD.
Subscribe
x
Subscribe for future updates
We will only send you emails about the update that you subscribe to, and you can unsubscribe at any time.