2.1 O&M Input on Design for New Building
Design for Maintainability emphasises the importance of timely integration of design and construction knowledge with O&M experiences into the project design in order to optimise building life.
Maintainability should be considered, and incorporated into the building system design, ensuring the ease, accuracy, safety, and economy of maintenance tasks within that system. Maintainability refers to the effectiveness and efficiency of maintenance activities. New working practices encouraged, such as Building Information Modelling for Asset Management (BIM-AM), require the involvement of asset owners and FMs to understand the information they require on handover. FMs should be involved during design stage and ensure the information handed over by the contractor fits their specific needs.
2.1.1 General Practice
2.1.2 Good Practice
2.1.3 Best Practice
2.2 Asset Information (Documentation)
Asset Information should be compiled, covering all major items of Lift & Escalator Installations in a format that is useful to the FM and Maintenance Service Provider. The information should be placed in readily accessible locations, and updated regularly with:
2.2.1 General Practice
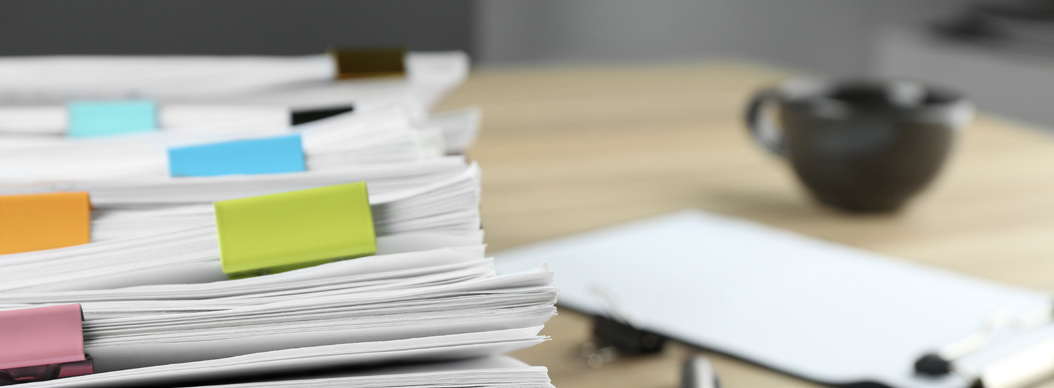
2.2.2 Good Practice
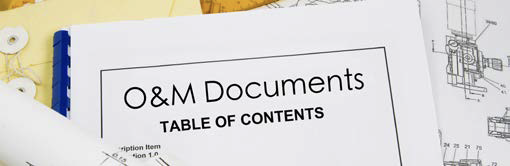
2.2.3 Best Practice
2.3 Operation Procedures
Operational efficiency refers to the lifecycle, cost-effective mix of preventive, predictive, and reliability-centred maintenance technologies, coupled with equipment calibration, tracking, and computerised maintenance management capabilities all targeting reliability, safety, occupant comfort, and system efficiency.
2.3.1 General Practice
2.3.2 Good Practice
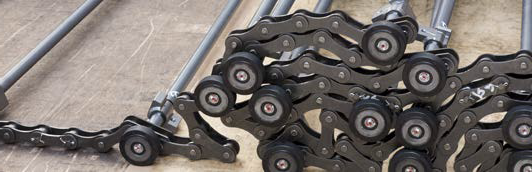
2.3.3 Best Practice
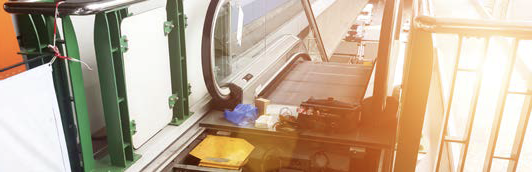
2.4 Emergency Preparedness
Building Emergency Preparedness is an effort to connect the emergency planning and response with the building users. The goal is to train personnel in basic emergency response actions, who know the building and occupants and can act as a resource and liaison to the stakeholders and building users.
An emergency action plan should identify all the potential hazards associated with the Lift and Escalator Installations, with a personnel responsibility matrix for allocating appropriate resources. The written plan should become an action document, updated according to an appropriate timeframe to ensure accurate information, such as updated contact information is provided.
2.4.1 General Practice
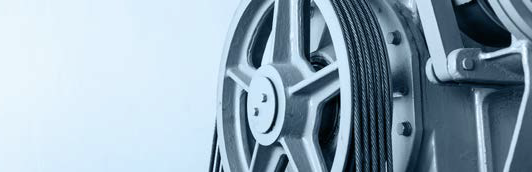
2.4.2 Good Practice
2.4.3 Best Practice
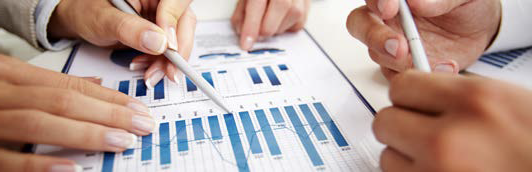
2.5 Preventive Maintenance Procedures / Standards
The goal of Preventive Maintenance is to prevent equipment failure caused by fatigue, neglect, or normal wear, through replacing worn components before actual failure. Planned Maintenance and Condition Based Maintenance activities include partial or complete overhauls at specified periods, and include oil changes, lubrication, minor adjustments, and so on. Typical procedures recommend that personnel record equipment deterioration upon any inspection to facilitate the replace or repair worn parts before any system failure.
The Preventive Maintenance Program must include the methodology and record for all actions that are necessary to maintain the optimal functioning of the Lift & Escalator Installations. The required maintenance procedures will be unique to each property and the systems within these facilities.
2.5.1 General Practice
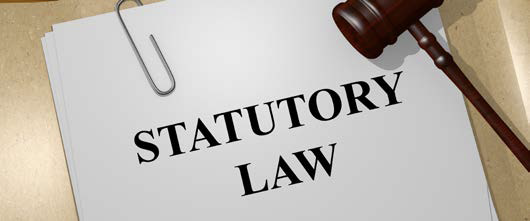
2.5.2 Good Practice
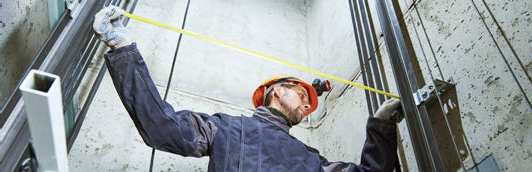
2.5.3 Best Practice
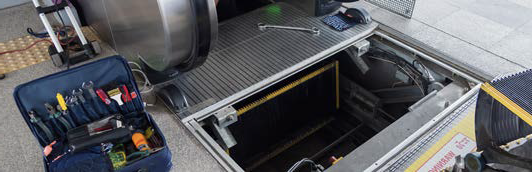
2.6 Corrective Maintenance
The goal of every maintenance team is to be fast and effective, especially when it comes to unexpected breakdowns of critical plant and equipment, aiming to achieve:
2.6.1 General Practice
2.6.2 Good Practice
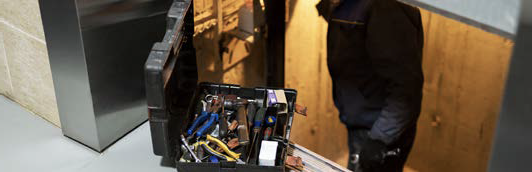
2.6.3 Best Practice
2.7 Maintenance Record Management
Good management of maintenance records is essential for ensuring that a piece of equipment is performing in line with the manufacturer’s warranty, and can help to determine its preventive maintenance schedule. It also assists service technicians in diagnosing repeat problems with a plant or equipment. Clear records can also provide assistance in legal proceedings, if ever necessary.
2.7.1 General Practice
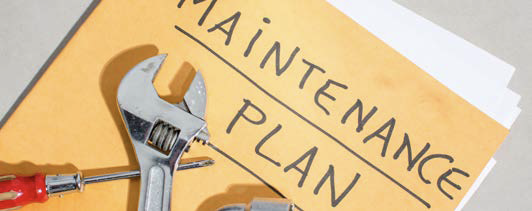
2.7.2 Good Practice
2.7.3 Best Practice
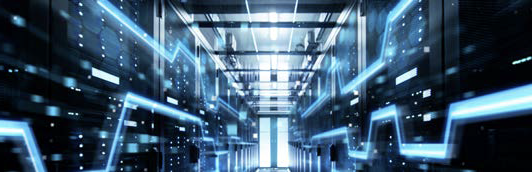
2.8 Spare Parts Management
Spare parts management refers to a systematic and structured way to store and extract spare parts efficiently for any maintenance activity. A good system should minimise downtime during service disruption and simplify equipment maintenance.
2.8.1 General Practice
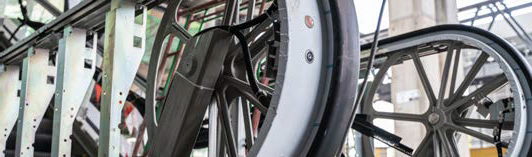
2.8.2 Good Practice
2.8.3 Best Practice
2.9 Addition, Alteration and Replacement (Planning and Implementation)
This includes the analysis, procurement, and management on additions, alterations as well as disposal and replacement of lift & escalator Installations to meet the organisational long-term objectives.
2.9.1 General Practice
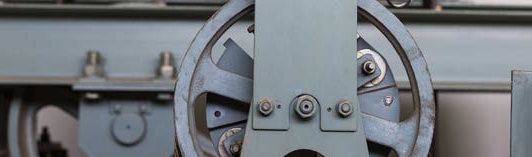
2.9.2 Good Practice
An alternative to determining the need for lift or escalator total replacement is to approach the Registered Lift or Escalator Contractor to provide professional recommendation, including studying the maintenance history, trend analysis of faults type and frequency, spare and defective part studies, computer modelling of lift or escalator replacement, etc.
2.9.3 Best Practice
2.10 Incident Management
Incident management refers to the "the combination of facilities, equipment, personnel, procedures and communications operating within a common organisational structure, designed to aid in the management of resources during incidents".
When a service is disrupted or fails to deliver the promised performance during service hours, it is essential to restore the service to normal operation as quickly as possible. In addition, any condition that has the potential to result in a breach or degradation of service ought to trigger a response that prevents the actual disruption from occurring. These are the objectives of incident management.
2.10.1 General Practice
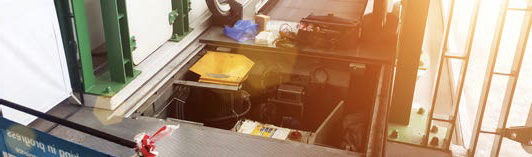
2.10.2 Good Practice
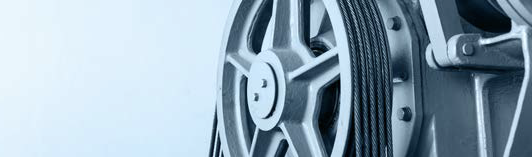
2.10.3 Best Practice
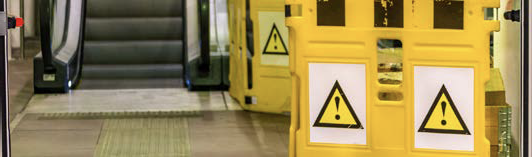
2.11 Environmental and Safety Management
Environmental and Safety Management ensures that operations are safe for all building users and visitors. Building Owners are obliged to implement all reasonable precautions to protect the environment, and maximise the building’s life cycle efficiencies.
2.11.1 General Practice
2.11.2 Good Practice
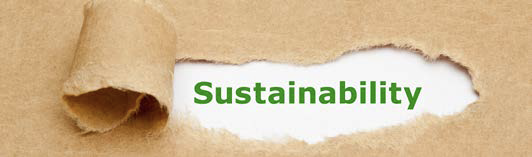
2.11.3 Best Practice
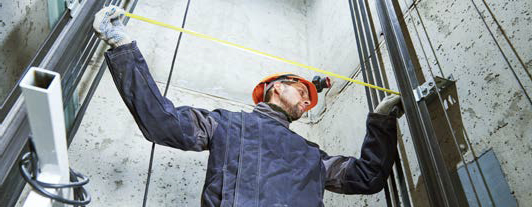
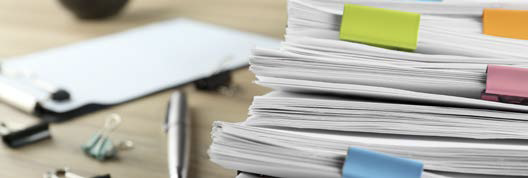
2.12 Application of Technologies
Technology and tools can be used to lower the cost of implementing and managing O&M best management practices.
2.12.1 General Practice
2.12.2 Good Practice
2.12.3 Best Practice
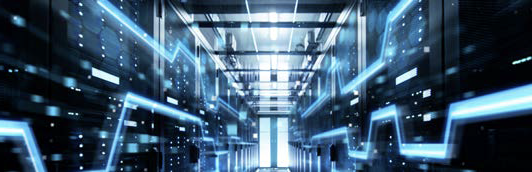
2.13 Stakeholder Management
Stakeholder management is a set of techniques that harnesses the positive influences and minimises the effect of the negative influences. It involves systematic identification, analysis, planning and implementation of actions designed to engage with stakeholders. Stakeholders are individuals or groups with an interest in the building or facility operation because they are involved in the work or affected by the outcomes. Most buildings or facilities and portfolios will have a variety of stakeholders with different, and sometimes competing, interests. These individuals and groups can have significant influence over the eventual success or failure of the work.
2.13.1 General Practice
2.13.2 Good Practice
2.13.3 Best Practice
2.14 Information Management
During the life of the system, the O&M Phase is the longest and most expensive and the information system provides the most value to the organisation in this phase.
2.14.1 General Practice
2.14.2 Good Practice
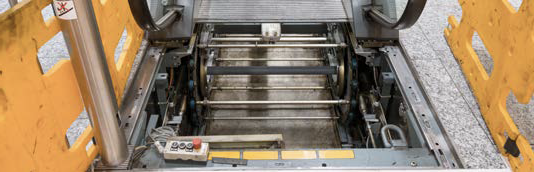
2.14.3 Best Practice
2.15 Structure and Qualification of O&M Team
Structure is the people, positions, procedures, processes, culture, technology and related elements that comprise the organisation. It defines how all the pieces, parts and processes work together. This structure must be totally integrated with the strategy defined for the organisation to achieve its mission and goals. Structure supports strategy. If an organisation changes its strategy, it must change its structure to support the new strategy. When it doesn’t, the structure acts like a bungee cord and pulls the organisation back to its old strategy.
2.15.1 General Practice
2.15.2 Good Practice
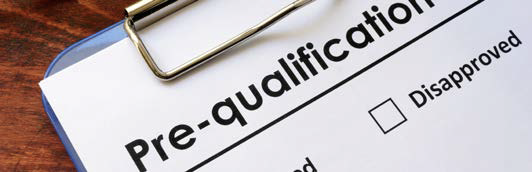