3. Innovative & Technology Initiatives
2.1 O&M Input on Design for New Building
Design for Maintainability emphasises the importance of timely integration of design and construction knowledge with O&M experiences into the project design in order to optimise building life.
Maintainability should be considered, and incorporated into the building system design, ensuring the ease, accuracy, safety, and economy of maintenance tasks within that system. Maintainability refers to the effectiveness and efficiency of maintenance activities. New working practices encouraged, such as Building Information Modelling for Asset Management (BIM-AM), require the involvement of asset owners and FMs to understand the information they require on handover. FMs should be involved during design stage and ensure the information handed over by the contractor fits their specific needs.
2.1.1 General Practice
2.1.2 Good Practice
2.1.3 Best Practice
2.2 Asset Information (Documentation)
Asset Information should be compiled, covering all major items of Lift & Escalator Installations in a format that is useful to the FM and Maintenance Service Provider. The information should be placed in readily accessible locations, and updated regularly with:
2.2.1 General Practice
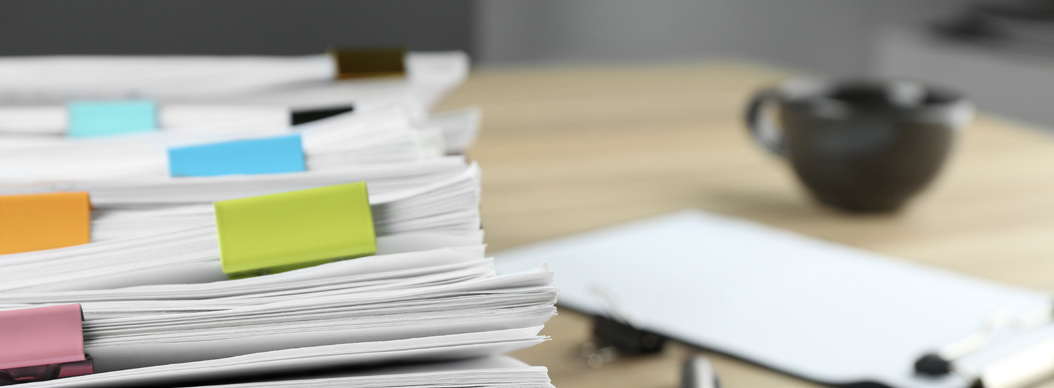
2.2.2 Good Practice
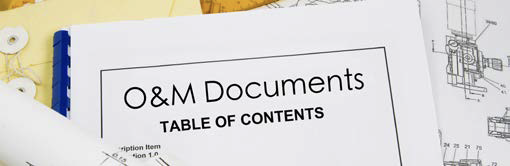
2.2.3 Best Practice
2.3 Operation Procedures
Operational efficiency refers to the lifecycle, cost-effective mix of preventive, predictive, and reliability-centred maintenance technologies, coupled with equipment calibration, tracking, and computerised maintenance management capabilities all targeting reliability, safety, occupant comfort, and system efficiency.
2.3.1 General Practice
2.3.2 Good Practice
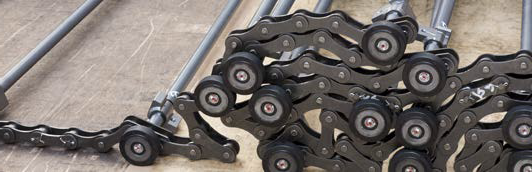
2.3.3 Best Practice
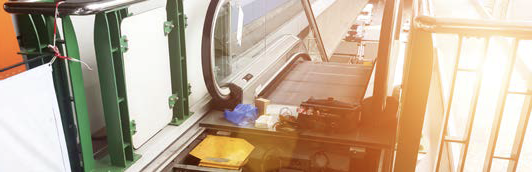
2.4 Emergency Preparedness
Building Emergency Preparedness is an effort to connect the emergency planning and response with the building users. The goal is to train personnel in basic emergency response actions, who know the building and occupants and can act as a resource and liaison to the stakeholders and building users.
An emergency action plan should identify all the potential hazards associated with the Lift and Escalator Installations, with a personnel responsibility matrix for allocating appropriate resources. The written plan should become an action document, updated according to an appropriate timeframe to ensure accurate information, such as updated contact information is provided.
2.4.1 General Practice
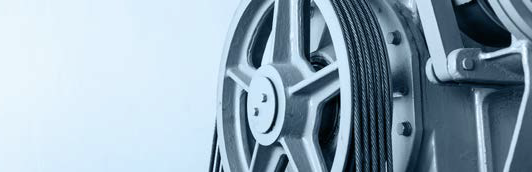
2.4.2 Good Practice
2.4.3 Best Practice
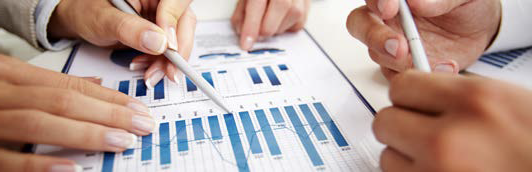
2.5 Preventive Maintenance Procedures / Standards
The goal of Preventive Maintenance is to prevent equipment failure caused by fatigue, neglect, or normal wear, through replacing worn components before actual failure. Planned Maintenance and Condition Based Maintenance activities include partial or complete overhauls at specified periods, and include oil changes, lubrication, minor adjustments, and so on. Typical procedures recommend that personnel record equipment deterioration upon any inspection to facilitate the replace or repair worn parts before any system failure.
The Preventive Maintenance Program must include the methodology and record for all actions that are necessary to maintain the optimal functioning of the Lift & Escalator Installations. The required maintenance procedures will be unique to each property and the systems within these facilities.
2.5.1 General Practice
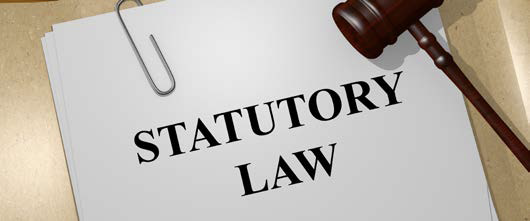
2.5.2 Good Practice
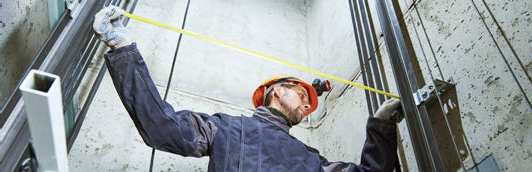
2.5.3 Best Practice
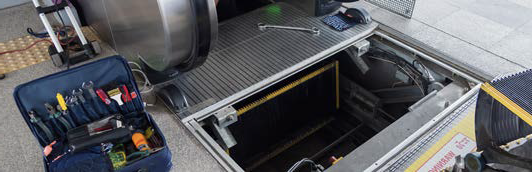
2.6 Corrective Maintenance
The goal of every maintenance team is to be fast and effective, especially when it comes to unexpected breakdowns of critical plant and equipment, aiming to achieve:
2.6.1 General Practice
2.6.2 Good Practice
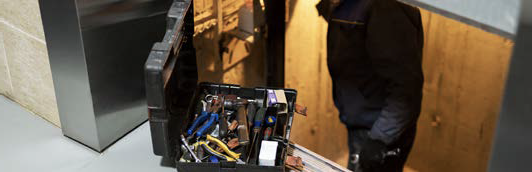
2.6.3 Best Practice
2.7 Maintenance Record Management
Good management of maintenance records is essential for ensuring that a piece of equipment is performing in line with the manufacturer’s warranty, and can help to determine its preventive maintenance schedule. It also assists service technicians in diagnosing repeat problems with a plant or equipment. Clear records can also provide assistance in legal proceedings, if ever necessary.
2.7.1 General Practice
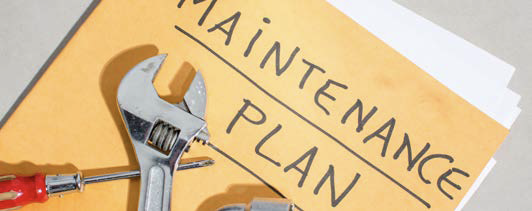
2.7.2 Good Practice
2.7.3 Best Practice
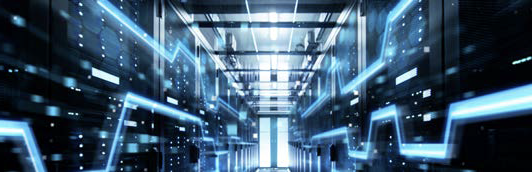
2.8 Spare Parts Management
Spare parts management refers to a systematic and structured way to store and extract spare parts efficiently for any maintenance activity. A good system should minimise downtime during service disruption and simplify equipment maintenance.
2.8.1 General Practice
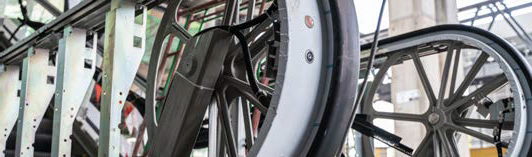
2.8.2 Good Practice
2.8.3 Best Practice
2.9 Addition, Alteration and Replacement (Planning and Implementation)
This includes the analysis, procurement, and management on additions, alterations as well as disposal and replacement of lift & escalator Installations to meet the organisational long-term objectives.
2.9.1 General Practice
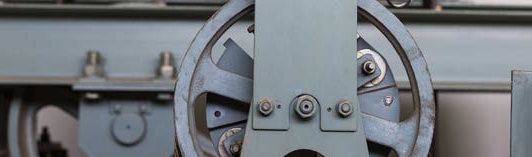
2.9.2 Good Practice
An alternative to determining the need for lift or escalator total replacement is to approach the Registered Lift or Escalator Contractor to provide professional recommendation, including studying the maintenance history, trend analysis of faults type and frequency, spare and defective part studies, computer modelling of lift or escalator replacement, etc.
2.9.3 Best Practice
2.10 Incident Management
Incident management refers to the "the combination of facilities, equipment, personnel, procedures and communications operating within a common organisational structure, designed to aid in the management of resources during incidents".
When a service is disrupted or fails to deliver the promised performance during service hours, it is essential to restore the service to normal operation as quickly as possible. In addition, any condition that has the potential to result in a breach or degradation of service ought to trigger a response that prevents the actual disruption from occurring. These are the objectives of incident management.
2.10.1 General Practice
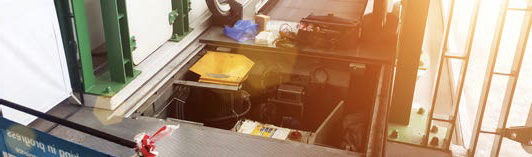
2.10.2 Good Practice
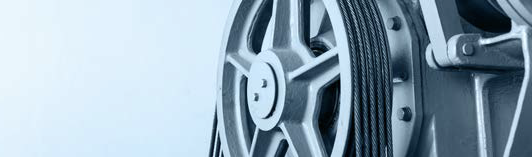
2.10.3 Best Practice
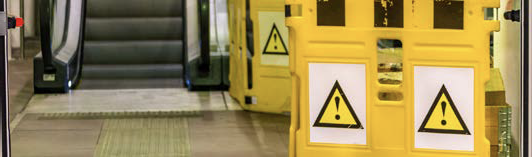
2.11 Environmental and Safety Management
Environmental and Safety Management ensures that operations are safe for all building users and visitors. Building Owners are obliged to implement all reasonable precautions to protect the environment, and maximise the building’s life cycle efficiencies.
2.11.1 General Practice
2.11.2 Good Practice
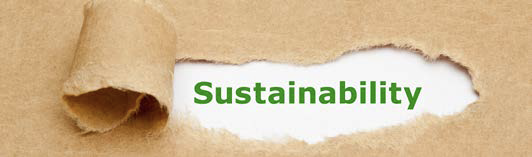
2.11.3 Best Practice
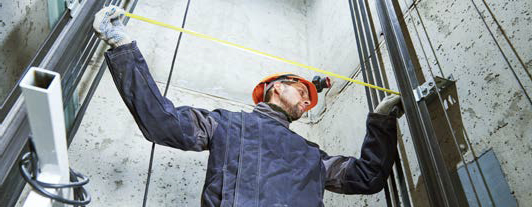
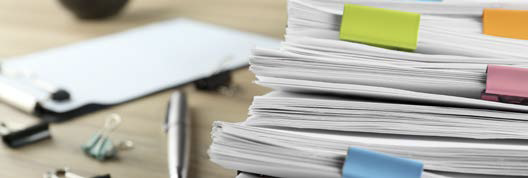
2.12 Application of Technologies
Technology and tools can be used to lower the cost of implementing and managing O&M best management practices.
2.12.1 General Practice
2.12.2 Good Practice
2.12.3 Best Practice
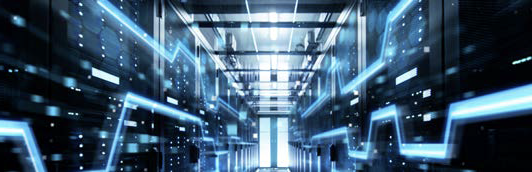
2.13 Stakeholder Management
Stakeholder management is a set of techniques that harnesses the positive influences and minimises the effect of the negative influences. It involves systematic identification, analysis, planning and implementation of actions designed to engage with stakeholders. Stakeholders are individuals or groups with an interest in the building or facility operation because they are involved in the work or affected by the outcomes. Most buildings or facilities and portfolios will have a variety of stakeholders with different, and sometimes competing, interests. These individuals and groups can have significant influence over the eventual success or failure of the work.
2.13.1 General Practice
2.13.2 Good Practice
2.13.3 Best Practice
2.14 Information Management
During the life of the system, the O&M Phase is the longest and most expensive and the information system provides the most value to the organisation in this phase.
2.14.1 General Practice
2.14.2 Good Practice
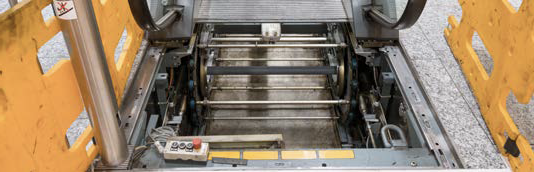
2.14.3 Best Practice
2.15 Structure and Qualification of O&M Team
Structure is the people, positions, procedures, processes, culture, technology and related elements that comprise the organisation. It defines how all the pieces, parts and processes work together. This structure must be totally integrated with the strategy defined for the organisation to achieve its mission and goals. Structure supports strategy. If an organisation changes its strategy, it must change its structure to support the new strategy. When it doesn’t, the structure acts like a bungee cord and pulls the organisation back to its old strategy.
2.15.1 General Practice
2.15.2 Good Practice
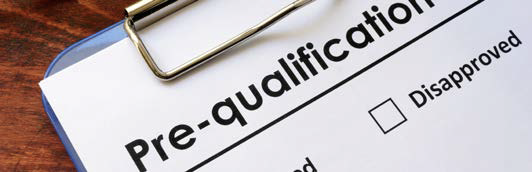
2.15.3 Best Practice
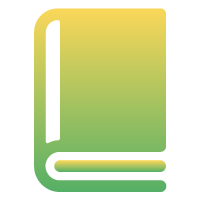
1.1 About This Best Practice Booklet
1.2 Target Audience
While in daily operations, the safety, system reliability, operational efficiency and sustainability of the assets rely on the daily operation and maintenance practices. In this regard, some information and recommendations to the interest of the trade stakeholders are outline in this Booklet as reference.
1.3 How to Use This Best Practice Booklet
• Operation and Maintenance and
• Alteration, Addition and Replacement.
The 15 key attributes are the key main considerations for achieving good or best performance in asset management of the lift and escalator Installations in buildings. Three levels of guiding principles, namely general, good and best practices, with associated examples of trade practices have been defined in each key attribute as reference. An additional chapter on “Innovative and Technology Initiatives” has also been included about the trend of technologies likely to be adopted to upraise the operation and maintenance service.
Level | Category | Description |
---|---|---|
Level 1 | General Practice | Involving general operating practices in fulfilling statutory requirements and aligning common practice in the trade industry |
Level 2 | Good Practice | Involving good operating practices with higher standard on enhancing either asset safety, system reliability, operational efficiency or sustainability |
Level 3 | Best Practice | Involving best operating practices with highest standard on asset management with use of innovative technologies or relevant life-cycle considerations |
The figure provides an illustrative map for the 15 key attributes in different sections of the booklet.
A summary of the contents in this booklet is as follows:
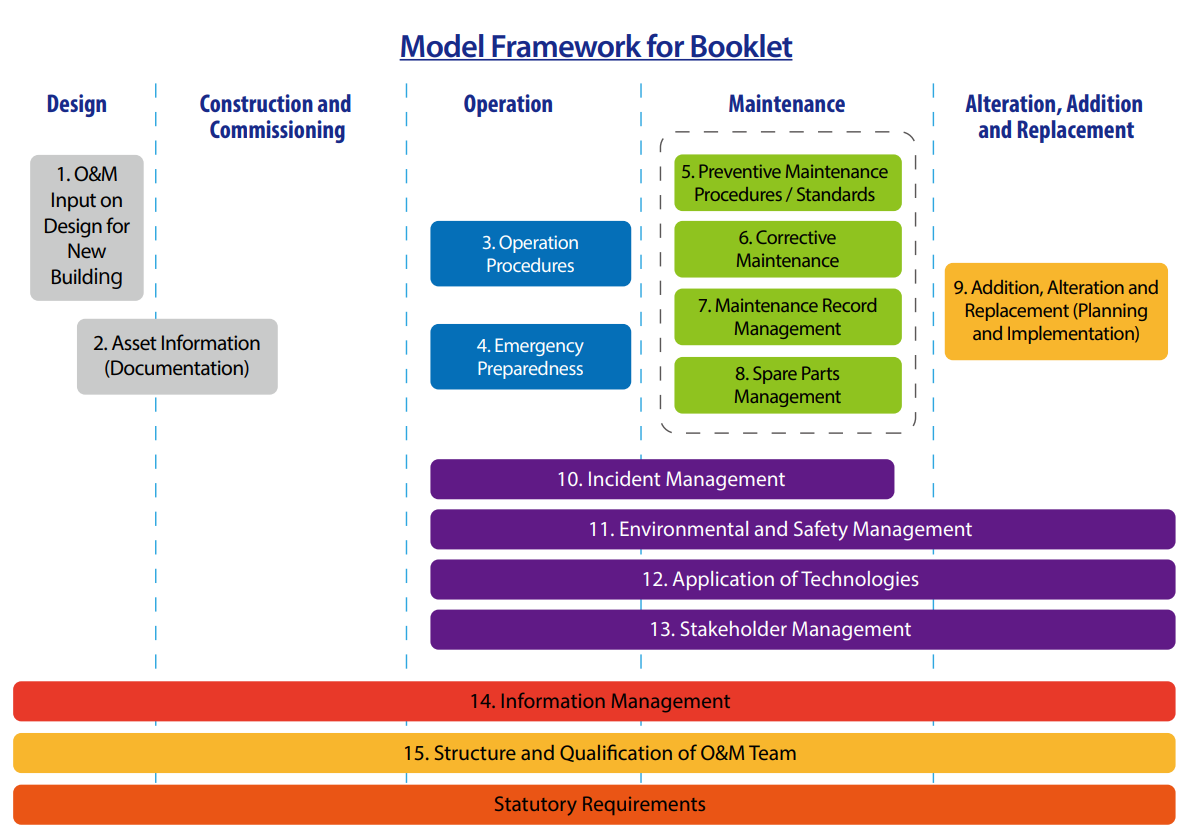
The 15 key attributes are:
- O&M Input on Design for New Building – It is important for Design Engineers to consider
accessibility and maintainability right from the planning and design of a facility, through its
life cycle.
- Asset Information (Documentation) – Good documentation is essential for facilitating good O&M.
This section describes the key documents that are required for the efficient O&M of Lift &
Escalator Installations.
- Operation Procedures - All activities associated with the routine, day to day use, support, and
maintenance of a building or physical asset; inclusive of normal/ routine maintenance. O&M
procedures at the system level do not replace manufacturers' documentation for specific pieces
of equipment, but rather supplement those publications and guide their use.
- Emergency Preparedness – Being prepared for emergencies is important, and emergency management
allow stakeholders to anticipate the types of potential hazards that could occur, and to think
of ways to reduce the impact.
- Preventive Maintenance Procedures / Standards- Preventive Maintenance consists of a series of time-based
maintenance requirements that provide a basis for planning, scheduling, and executing scheduled
(planned versus corrective) maintenance. It is of a planned nature (versus the unplanned nature
of Corrective Maintenance (CM)).
- Corrective Maintenance – This is an essential maintenance task performed to correct failures,
breakdowns, malfunctions, anomalies or damages detected during inspections, or through
monitoring, alarming, or reporting, or any other source. The actions taken will aim to restore
plant and equipment back into regular and required operation mode.
- Maintenance Record Management – This is a key part requiring efficient storage and management.
Proper maintenance records minimise the number of expensive repairs, increase safeness in
operation and enhance the visibility of equipment health.
- Spare Parts Management – Managing spare parts in an optimal way is an inherent and substantial
part of O&M aimed at ensuring that spare parts are available in a timely manner for corrective
maintenance in order to minimise the downtime of a system or equipment.
- Addition, Alteration and Replacement (Planning and Implementation) - This includes the
analysis, procurement, management on additional, alteration as well as disposal and replacement
of assets to meet the organisation’s long term aims and objectives.
- Incident Management – This is the essential process to restore normal service operation as
quickly as possible and limit the potential disruption caused by an incident.
- Environmental and Safety Management - The Building Owner has the ultimate legal and moral
responsibility to ensure the health and safety of people in and around the building and for the
protection of the environment around it.
- Application of Technologies - Integration and adaptation of new technologies with innovative
methods to optimise system performance as well as operational effectiveness.
- Stakeholder Management – This is a critical component to the successful delivery of any
service. It allows the correlation of stakeholders with potential known triggers, such as
disruptions to their normal patterns and update on work progress, etc. It also estimates the
impact that these reactions may have on your project or strategies and identifies whether
targeted communication, mitigation or an alternative solution is required.
- Information Management – This concerns a cycle of organisational activity: involving the
acquisition of information from one or more sources, and the custodianship and distribution of
that information to those who need it.
- Structure and Qualification of O&M Team - It is of critical importance that all O&M teams have a proper structure and their personnel have the relevant qualifications to perform the works in a safe, responsible and accountable manner.
1.4 Stakeholder Responsibilities
It is essential that all involved stakeholders shall work collaboratively as a team. While those involved for improving the current practices, they shall commit to facilitate and provide sharing on the necessary training, practical experience, knowhow and awareness of modern technology and the skills of optimising performance in their organisations.
The Building Owner should motivate and empower all Stakeholders to deliver efficiencies through O&M practices. The policies and strategies set by the Building Owner should drive the process for setting up the implementation of maintenance contracts and efficiency measures.
Tenants should adhere to the lease conditions when available, including Green Leases and Tenancy Fit-Out Guidelines, that express mutual expectations between Building Owners and Tenants with regards to operation, maintenance and performance requirements of buildings. They should observe the statutory requirements and use the lift and escalator properly. When use of the lift or escalator is prohibited, anyone who uses the lift or escalator regardless of warning is in breach of the law.
It is important for the FM to develop a maintenance regime that is geared towards delivering good outcomes in partnership with Maintenance Service Providers, who would benefit from the enhanced system efficiency. Forming good relationships and ensuring effective channels of communication including good documentation, is an important aspect to the process.
The operation and maintenance of buildings have already been facing several critical challenges, including the aging workforce, aging assets and climate change. The new generation of smart technologies such as artificial intelligence, asset management Internet of Things, building management system, building information system or even specialised drone-enabled automation applications would have brought further challenges to us with safety and well-being of occupants and visitors inside buildings elevated to a completely new level. Building O&M practitioners shall endeavour to adopt innovations, technologies and best practices/guidelines to improve the management of E&M assets, thereby enhancing the resilience and intelligence of government buildings.
Below are five emerging technology trends that may have impact on facilities management industry.
3.1 Technology Trend 1: CAFM Software
In the current dynamic market, computer aided facility management (CAFM) software is highly important for facilities manager in the workplace. Tasked with many responsibilities, facilities manager require complete day-to-day functionality by integrating technology, processes, and people. With the help of CAFM software, facilities manager can better execute daily operational responsibilities from monitoring and managing customer service requests to preventive maintenance and operational facility services.
3.2 Technology Trend 2: Building Information Modelling (BIM)
Although not a new technology, Building Information Modelling-Asset Management (BIM-AM) is a tool used by contractors and architects to develop and scale virtual models of building projects. Giving building owners and operators a complete visual model of the facility prior to construction, it provides valuable insights into project delivery timelines and budgets.
When integrated with existing work order programs or facility maintenance software, BIM delivers on improved floor plans, asset information and financial estimates. As the technology continues to evolve, the importance of BIM in facilities management will continue to grow.
3.3 Technology Trend 3: Internet of Things (IoT)
The Internet of Things (IoT) refers to the network of internet accessible devices utilised by organisations. Relying on tools such as sensors, thermostats and actuators to evaluate data and reduce the amount of energy used for tasks, IoT systems effectively reduce energy bills and provide insightful data to improve efficiency within all facilities. With various sensors generating data, facilities management organisations are able to identify issues and potential problems faster and easier.
3.4 Technology Trend 4: Drones
Drones are unmanned aerial vehicles (UAVs) that have the ability to improve efficiency in facilities management. Some of these opportunities include safety in inspections, and the automation of delivery services. Still in its infancy, there is no disputing that sending a drone equipped with a high-resolution camera is a quicker and safer way to evaluate a building’s exterior than sending a member of the team.
3.5 Technology Trend 5: Artificial Intelligence (AI)
Artificial intelligence (AI) is the broader concept of machines being able to carry out tasks in a smart manner. AI also refers to machines imitating and bettering human performance. More adaptive than traditional systems, AI holds an array of capabilities for enhanced performance in the facilities management industry. A part of AI, machine learning is a current application that provides machines access to data and allows them to draw insights on their own. With machine learning, facilities management organisations can better predict how much time an asset, such as a building, has before its performance degrades or fails. From online chatbots in customer service to finding patterns in historical data through the use of algorithms, AI will expand and benefit all departments within an facilities management organisation.
3.6 Technology Initiatives
Based on the above five technology trends, the technology initiatives in respect of the 15 key attributes are summarised below for reference
O&M Aspect | Feasible Initiatives | Reference |
---|---|---|
O&M Input on Design for New Building | a) Simulate best practice O&M activities using BIM or other simulation software to understand operability and maintainability before construction. | • BIM for Facility Managers issued by International Facility Management Association (IFMA) • BIM-AM Standards and Guidelines issued by EMSD • Housing Authority BIM Standards and Guidelines |
Asset Information (Documentation) | a) Adopt computerised asset information model such as BIM to maintain all asset information under an efficient asset management system; b) Inspect, digitise and upkeep latest record and logbook for Fire Services Installations and equipment on a regular basis; c) Implement mobile solutions for asset management record retrieval and updating of records, e.g. O&M manual, fault history, etc.; d) Adopt Radio Frequency Identification (RFID) or QR codes for asset management. | • BIM for Facility Managers issued by (IFMA) • BIM-AM Standards and Guidelines issued by EMSD • Construction Industry Council BIM Standards |
Operation Procedures | a) Adopt cloud-based technology to store information of Lift and Escalator Installations and equipment to be accessed by property management personnel when needed; b) Implement IoT-enabled self-diagnosis function for the healthiness of major Lift and Escalator equipment; c) Incorporate on-line condition monitoring and mobile technologies on Lift and Escalator systems to improve maintenance and reduce downtime. | |
Emergency Preparedness | Nil | |
Preventive Maintenance Procedure / Standards | a) Conduct predictive maintenance based on data analysis on fault history and equipment condition. | |
Corrective Maintenance | Nil | |
Maintenance Record Management | a) Adopt computerised monitoring system to maintain detailed maintenance information with capability for prompt alert, review and further analysis. The system at least contains the following information for weekly updates by designated person(s): • Maintenance contractor's organisation chart and contact list • Monthly fault call and emergency repair reports • Daily fault call progress report • Details of corrective maintenance • Equipment breakdown report • Working programme for maintenance, annual inspections and tests, overhaul, drills, safety inspections and any other scheduled works • Preventive maintenance schedule • Details of preventive maintenance completed • Spare part list • Registers of tools, equipment, materials, spare parts and instruments as well as calibration certificates of instruments • Record of plants and equipment details • Overhaul reports • Record of statutory submission • Any other useful information (e.g. site photos) | O&M Input on Design for New Building |
Spare Parts Management | a) Utilise an automatic inventory control system using AI to manage spare parts inventory by prediction of spare parts requirement using AI for advance and on-time spare parts procurement. | |
Incident Management | a) Consider advance management tools to help optimise system performance, e.g., BIM – asset registers, equipment life-cycle track, system configuration, critical device status, maintenance history, installation visualisation, etc.; b) Adopt IoT technologies to allow quicker and instant reporting and maintenance data collection for future improvement. | |
Addition, Alteration and Replacement (Planning and Implementation) | a) Adopt advance management tools such as integrated facility management tools to allow a quick search of all equipment information and records, to enhance effectiveness of overall planning. | |
Environmental and Safety Management | a) Adopt recycled components or equipment for the maintenance / repair / replacement works; | |
Application of Technologies | a) Adopt application of AI, big data analysis, IoT etc.; b) Knowledge transfer from research to industry to Interface Science / Technology. | |
Stakeholder Management | a) Establish a smart system to automatically notify stakeholders on upcoming schedules and progress of all O&M activities, addition, alteration and replacement works. | |
Information Management | a) Establish an integrated management system (iBMS); b) Create centralised database for automatic replacement planning for equipment; c) Establish an online real time server for storing maintenance related information through mobile devices; d) Provide online access of all information for maintenance party during preventive maintenance works. | |
Structure and Qualification of O&M Team | Nil |
4. Industry Standards and Requirements
4.1 Guidance Notes and Codes of Practice
The readers may refer to the prevailing statutory requirements, websites of the Controlling Authorities and following documents for further information on the relevant specific requirements:-
4. Industry Standards and Requirements
4.2 International Standards
The readers may refer to the prevailing international standards as accepted by the Controlling Authorities or the approval standards for existing buildings:-
5. Useful Forms/ Check List – Samples
5.1 Check List for Periodic Maintenance of a Lift
For keeping the lift and its associated equipment or machinery in safe working order, at least the following applicable items are to be checked for proper condition, and attended to if necessary, in accordance with schedule recommended by the lift manufacturer :
Maintenance Items | Examples of checks |
---|---|
a)
Lift machine gearbox and bearing
|
Check condition |
b)
Traction Machine, including motor shaft, bolts connection worm gear and flange of the
traction sleeve
|
Check operation Check bearing for wear Check lubrication |
c)
Brake
|
Check braking system Check part for wear Check stopping accuracy |
d)
Overspeed Governor and tension pulley
|
Check moving parts for free movement and wear Check operation Check switch |
e)
Drum, sheaves, grooves of sheaves and pulley
|
Check condition and grooves for wear |
f)
Commutators and slip rings of motor generator set
|
Check condition |
g)
Controllers contact, interlock and dashpots
|
Check cabinet is clean, dry and free from dust |
h)
Floor selector generator set
|
Check operation |
i)
counterweight guide shoes and lubricatorsand pulley
|
Check Guideshoes, rollers for wear Check fixings Check lubrication where necessary |
j)
lift well cleanliness and condition of lift well enclosure
|
Check cleanliness and condition of lift well enclosure |
k)
guides and fixings
|
Check for deterioration and wear |
l)
limit switches, direction switches and their operating devices
|
Check operation |
m)
car door and landing door
|
Check door closed contact or lock Check doors for free running Check door guiding Check door gaps Check wire rope or chain when used for integrity Check passenger door protective device Check lubrication |
n)
car guide shoe and lubricators, tensioning devices and door operating gear
|
Check operation |
o)
any irregularities in starting, stopping and general running of the lift
|
Check operation |
p)
car controls, car door switches, safety edges, emergency stop, alarm bell and intercom
system; condition of car body fixing, car interior and floor covering; car lighting, car
ventilation and levelling accuracy
|
Check operation |
q)
landing buttons, indicators, and fireman's lift switch
|
Check operation |
r)
door-lock operation including electrical and mechanical interlocks for car door and landing
door
|
Check operation |
s)
suspension ropes, compensation ropes/ chains, their anchorages and rope retainer (rope
guard)
|
Check for wear, elongation and tension Check lubrication only where intended |
t)
slack rope switch, safety gear switch, broken tape or rope switch and overspeed governor
switch
|
Check operation |
u)
counterweight clearances for rope stretch; rope equaliser; filler weight fixings; and
safety gear for guide clearance and free movement
|
Check operation |
v)
buffer condition
|
Check oil level Check lubrication Check switch when fitted Check fixings |
w)
travelling cables and their anchorages
|
Check operation |
x)
safety notices and signs
|
Check condition |
Note In addition to the items listed in the maintenance schedule/instructions provided by the lift manufacturer, the RC responsible for maintaining the lift shall also carry out the following maintenance items for not less than twice a year if the concerned lift does not equipped with unintended car movement protection device, ascending car overspeed protection device or double braking system. The following maintenance items shall be completed in one single maintenance visit. |
|
a)
Disassembly maintenance of the braking mechanism for the lift machine brake.
|
The RC shall ensure that the relevant components of the brake (e.g. brake lining, solenoid plunger, brake spring, etc.) are in good and safe working order and ensure that all levers and moving parts of the brake must be kept clean with smooth operation and properly lubricated, and the relevant parts of the brake replaced in accordance with the manufacturer's instructions. |
b)
Measure the braking distance
|
Measure the braking distance by performing no-load brake test to ensure compliance with the lift manufacturer's requirements. |
c)
Measure grooves of traction sheave in the lift traction machine and replace the traction
sheave in accordance with the manufacturer's requirements.
|
Perform no-load traction test for the lift and measure the leveling accuracy to ensure the traction and leveling accuracy are in compliance with the lift manufacturer's requirements. |
d)
Check the mechanical locks and electrical contacts of all lift landing doors to ensure they
are in safe working order.
|
Check operation |
5. Useful Forms/ Check List – Samples
5.2 Check List for Periodic Maintenance for a Hydraulic Lift
In addition to the check list for the electric lift, at least the following applicable items which are pertinent to a hydraulic lift should be checked and attended to –
Maintenance Items | Examples of checks |
---|---|
a) ram and cylinder condition | Check for oil leakage |
b) levelling switches | Check operation |
c) pipework, joints, bolts and fixings; stop valve; oil reservoir; pump and motor | Check Condition |
d) control valves, pilot and levelling valves; overrun and cut-off devices; overload relief valve | Check Condition |
e) air release cock and anti-syphon valvey | Check condition |
f) Oil tank | Check hydraulic fluid level, adjusted to within the margin set by the manufacturer, written record should be kept as to the quantity of hydraulic fluid added to the system. Check tank and valve unit for leakage |
g) Gland packings and seals – where gland packing or seals are used for valves and cylinders | Examine and maintain in accordance with manufacturer’s recommendations to prevent excessive loss of hydraulic oil. |
h) Relief valve | Check to ensure that the seal is intact. |
5. Useful Forms/ Check List – Samples
5.3 Check List for Periodic Maintenance of an Escalator
For keeping the escalator and its associated equipment or machinery in safe working order, at least the following applicable items are to be checked for proper condition, and attended to if necessary, in accordance with a schedule recommended by an escalator manufacturer :
Maintenance Items | Examples of checks |
---|---|
a) clearances between consecutive steps/ pallets and between the steps/pallets and the skirt panels | Check clearances and operation |
b) drums, pulleys and moving parts | Check operation |
c) machine room cleanliness | Check condition |
d) any irregularities in running the escalator/ passenger conveyor | Check operation |
e) safety devices, such as skirt panel switches, handrail inlet switches, emergency stop switches, broken drive/step chain devices, overspeed governor, speed monitoring device that for detection of overspeed or unintentional reversal of the direction of travel, step sagging devices, missing step devices, comb plate switches, etc. | Check condition |
f) main drive system including drive chain and sprocket | Check condition Check for tension and wear Check bearing for wear Check lubrication |
g) step/pallet rollers and step/pallet chain | Check for tension and wear Check lubrication |
h) handrail | Check for free running and condition Check tension Check synchronisation between step/pallet band and the handrail |
i) operational brake and auxiliary brake (if equipped) including their braking efficiencies | Check braking system Check parts for wear |
j) comb | Check condition Check meshing with step s. pallets or belt |
k) lubricating pump and oil | Check operation |
l) motor gear box | Check gear and associated parts Check lubrication |
m) lighting system | Check operation |
n) floor intersection guards and any safeguards against adjacent building obstacles from causing injury to users | Check condition |
o) safety notices and signs | Check condition |